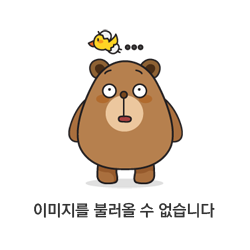
Total Productive Maintenance (TPM)
Introduction
Total Productive Maintenance (TPM) is a Lean Manufacturing technique that is used to improve the overall efficiency and effectiveness of manufacturing processes. TPM involves a collaborative approach to maintenance that involves all stakeholders in a manufacturing process, including operators, maintenance personnel, and management.
Key Principles of TPM
- Total Employee Involvement: TPM involves the participation of all employees in the maintenance process.
- Focused Improvement: TPM focuses on continuous improvement of equipment and processes.
- Early Equipment Management: TPM emphasizes early management of equipment to prevent problems and minimize downtime.
- Quality Maintenance: TPM prioritizes quality maintenance to improve the quality of products and processes.
- Safety, Health, and Environment: TPM incorporates safety, health, and environmental considerations into the maintenance process.
Benefits of TPM
- Improved Equipment Reliability: TPM leads to improved reliability of manufacturing equipment through regular maintenance and continuous improvement.
- Increased Equipment Availability: TPM results in increased availability of manufacturing equipment by reducing downtime and maximizing production time.
- Enhanced Quality: TPM leads to enhanced quality of products and processes through improved maintenance and continuous improvement.
- Improved Productivity: TPM results in improved productivity through reduced downtime and improved efficiency.
- Enhanced Employee Involvement: TPM leads to enhanced employee involvement in the maintenance process, which can lead to increased motivation and job satisfaction.
Implementing TPM
- Assess Current Maintenance Processes: The first step in implementing TPM is to assess the current maintenance processes to identify areas for improvement.
- Develop a TPM Implementation Plan: Based on the results of the assessment, a TPM implementation plan should be developed that outlines the steps to be taken to implement TPM.
- Train Employees: All employees involved in the maintenance process should be trained in the principles and practices of TPM.
- Implement TPM: The next step is to implement TPM in the manufacturing process.
- Monitor and Review: The final step is to monitor and review the implementation of TPM and make adjustments as needed to optimize the maintenance process.
Conclusion
Total Productive Maintenance (TPM) is a Lean Manufacturing technique that is used to improve the overall efficiency and effectiveness of manufacturing processes. TPM involves a collaborative approach to maintenance that involves all stakeholders in a manufacturing process, including operators, maintenance personnel, and management. The key principles of TPM include total employee involvement, focused improvement, early equipment management, quality maintenance, and safety, health, and environmental considerations. The benefits of TPM include improved equipment reliability, increased equipment availability, enhanced quality, improved productivity, and enhanced employee involvement. To implement TPM, it is important to assess current maintenance processes, develop a TPM implementation plan, train employees, implement TPM, and monitor and review the implementation.
comment